Accio - Brettnurflügel
Nach dem Sif (Jupp Wimmer) wollte ich mal wieder was in GFK machen. Beim Accio geht es mir darum, auf einem Rumpf verschiedene Tragflügel ausprobieren zu können. Auch, wenn ich überwiegend am Hang fliegen will, soll eine Motorisierung möglich sein.
Spannweiten zwischen 1800mm und 3000mm sollten möglich sein.
Daraus ergibt sich für den Rumpf:
- Seitenruder sollte groß genug sein, um auch eine große Spannweiten zu unterstützen. Ich habe mich dann aber an der Seitenrudergröße des Amokka-Wood orientiert.
- Es sollten unterschiedliche Profile möglich sein
- Vorne muss der Rumpf einen kreisförmigen Querschnitt haben, damit für den Antrieb ein Spinner passt. Bei einem ovalen Querschnitt sieht das blöd aus
- Quesrschnitt so klein wie möglich, aber 3S/1300mAh LiPos sollten gerade noch reinpassen
Schulterdecker
Wegen der unterschiedlichen Profile kann man keine Profilanformung am Rumpf machen. Aber einfach nur flache Seitenflächen sehen auch nicht gut aus. Somit wird die Tragfläche von oben aufgeschraubt. Der Vergleich der verschiedenen Profilunterseiten zeigt, dass es noch Raum für Variationen gibt.
Nur das PW51 (gestrichelt gezeichnet) und die verschiedenen Profile von Wolfgang Werlings Hai Familie passen eher nicht. Da müsste ich dann an der Tragfläche etwas anpassen.
So sieht das dann in der CAD aus:
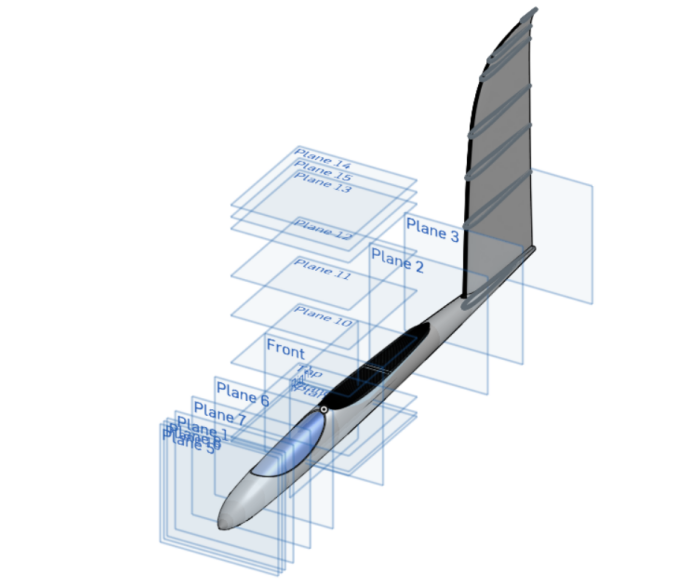
Dass erste Muster in ganz klein:
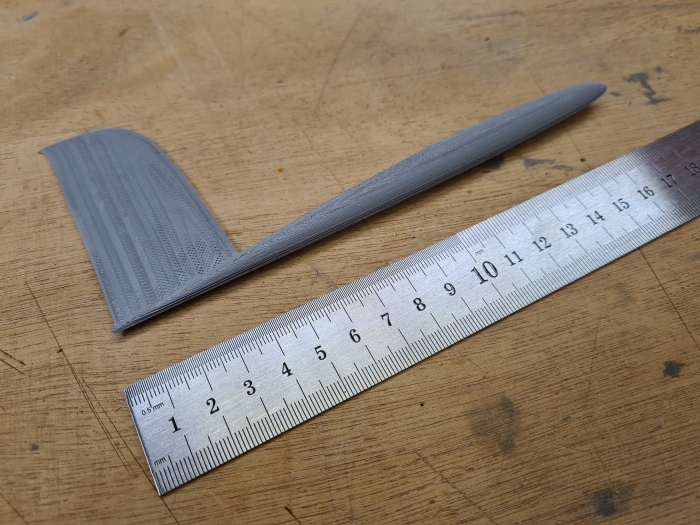
Urmodell
Diesmal sollte es ein Urmodell aus PLA aus dem 3D-Drucker werden, von dem die Formen dann abgeformt werden. Um es vorweg zu nehmen:
+ Das Schleifen ist einfacher auf dem Urmodell verglichen mit der Innenseite einer 3D-gedruckten Form
+ Vermutlich ist die Form haltbarer
- Das sind noch mal ein paar Arbeitsschritte mehr, die sich nicht unbedingt lohnen, wenn man eh nur eine handvoll Rümpfe macht.
Vermutlich wird das nächste Projekt wieder aus einer 3D-gedruckten Form kommen...
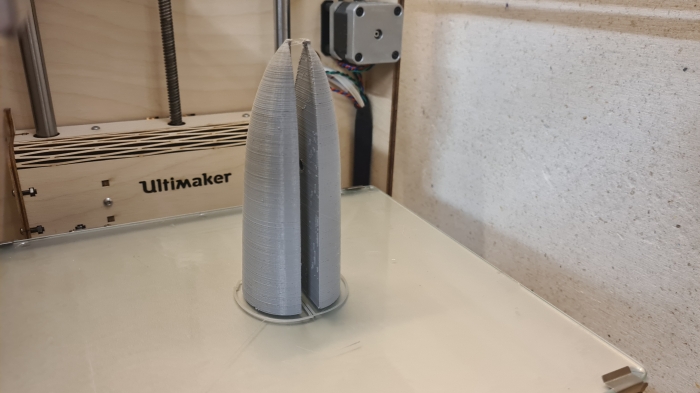
Die beste Qualität erhält man, wenn man aufrecht druckt (hier übrigens nicht so gut, weil der Ultimaker nicht sauber extrudiert hat). Leider geht das beim Seitenleitwerk nicht.
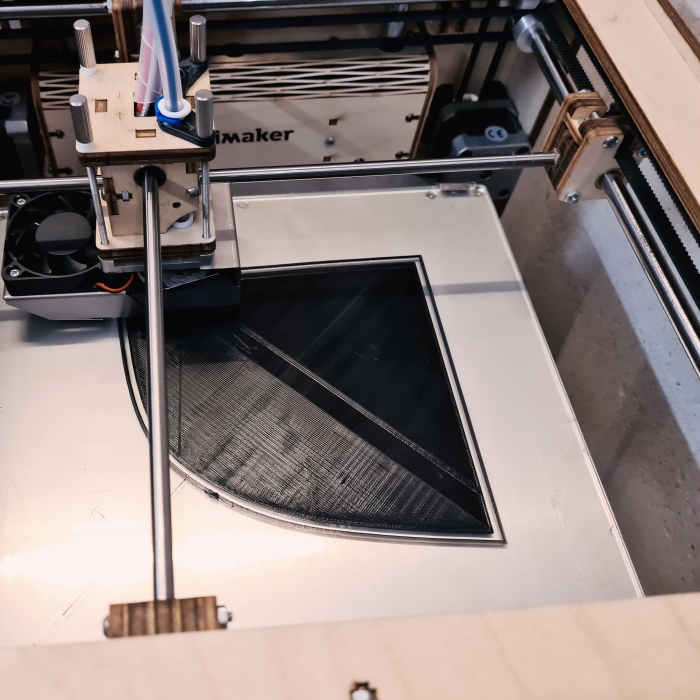
Da der Rumpf etweas über 600mm lang ist, geht das natürlich nur aus mehreren 3D-Druck-Teilen:
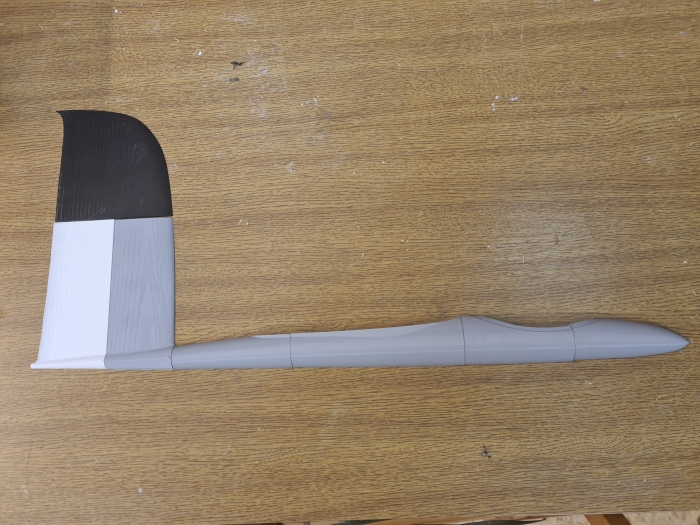
Nach Spritzen, Spachteln und Schleifen
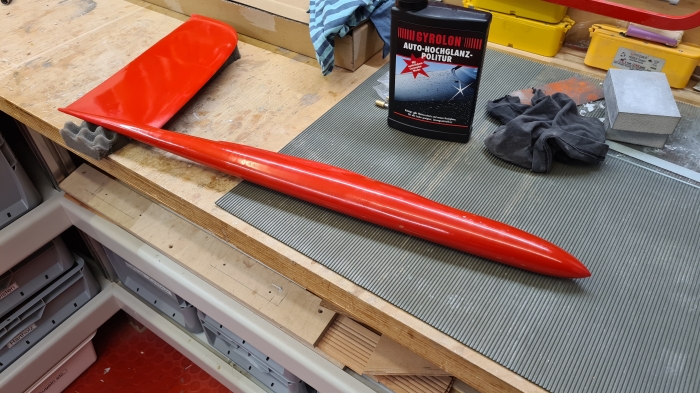
Rumpfform
Die Trennebene habe ich aus einem Teil Makrolon gefräst. Hierzu konnte ich die CAD-Daten des Onshape-Entwurfs verwenden, was einen passgenauen Ausschnitte garantiert.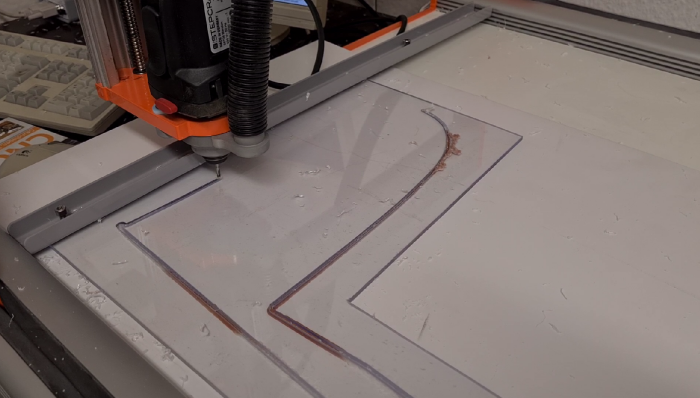
Damit der Rumpf mittig in der Trennebene liegt, habe ich Halterungen gedruckt:
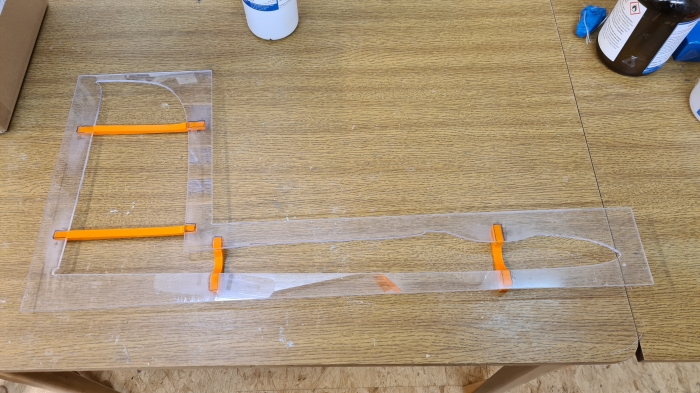
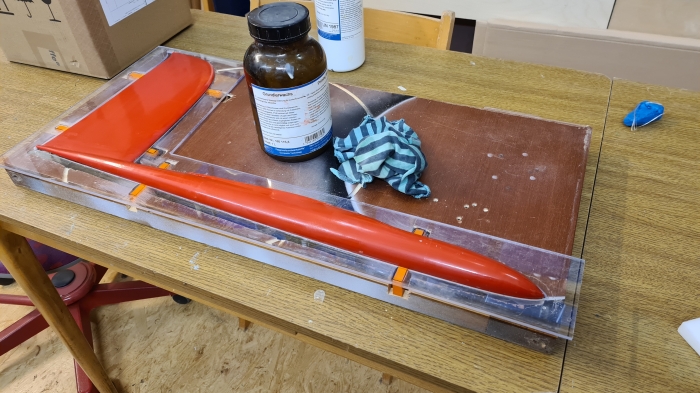
Nach gründlichem Wachsen und der Behandlung mit Folientrennmittel PVA kommt das Formenharz und ein paar Lagen Glasfilamentgewebe drauf.
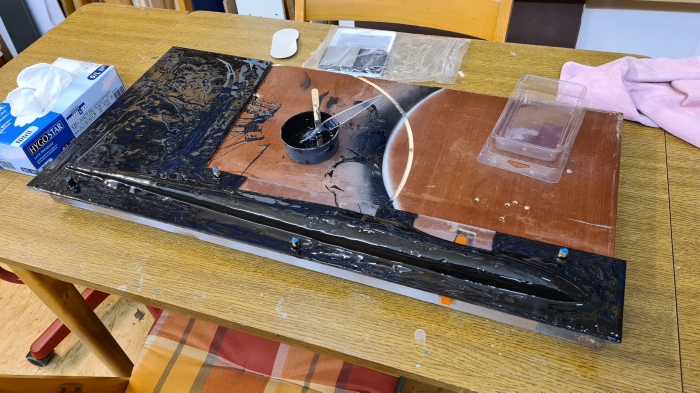
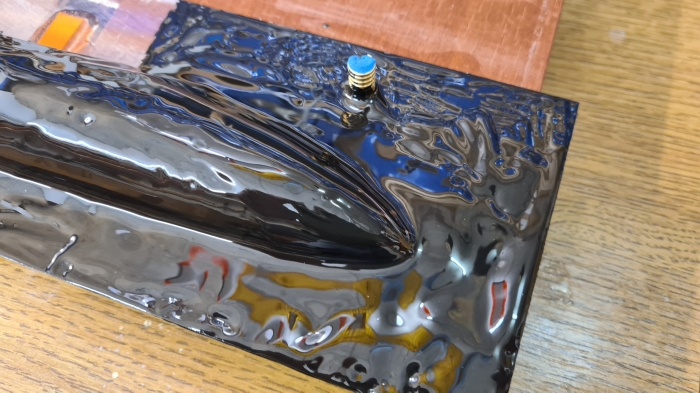
Die erste Hälfte ist geschafft:
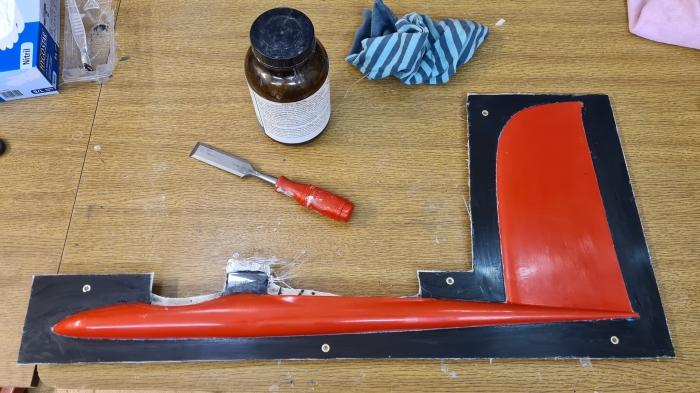
Und nachdem ich den Vorgang mit der zweiten Seite wiederfolt habe, liegen zwei Formhälften vor mir. Im Bild übrigens der Rumpf des SimpleX, bei dem ich die Rumpfform gedruckt habe.
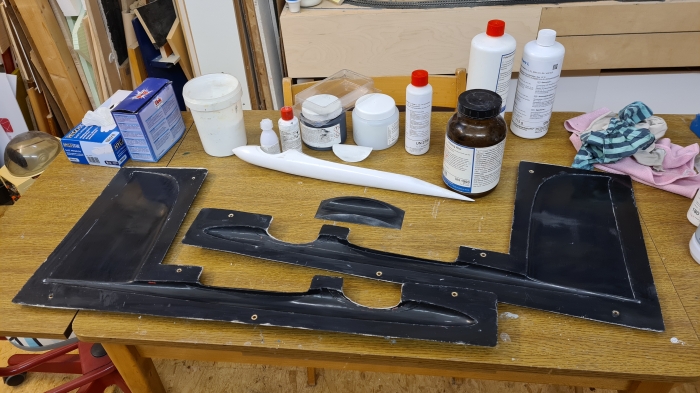
Der erste Rumpf
Den habe ich mit einem transparenten Gelcoat gemacht, damit ich besser sehe, ob alles durchtränkt ist. Zukünftige Rümpfe erhalten dann aber ein weiß eingefärbtes Gelcoat.Vom Laminieren habe ich keine Fotos. Es geht los mit dem Öffnen der Form:
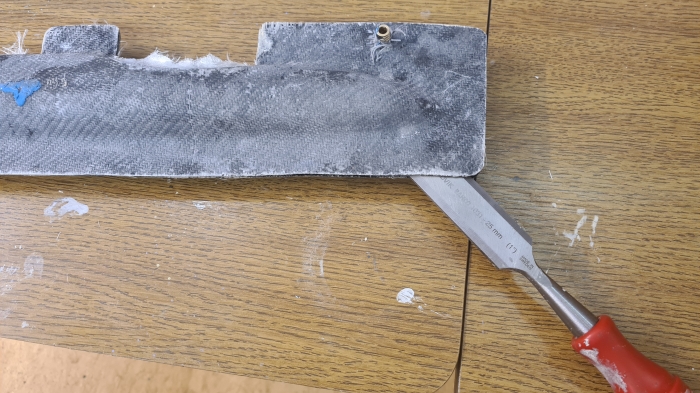
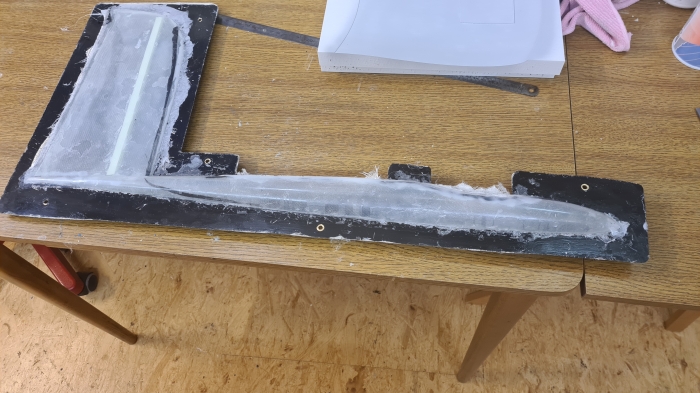
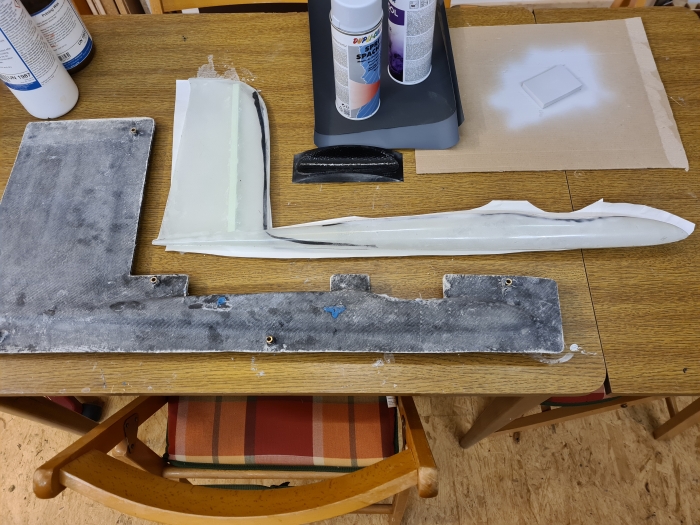
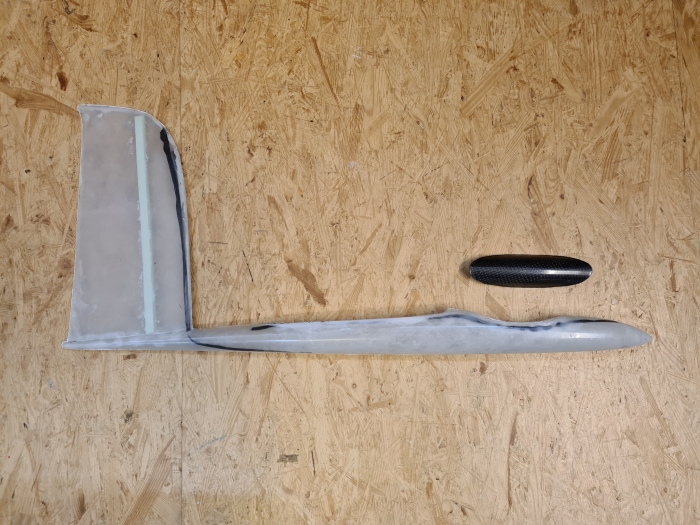
Haubenform aus dem 3D-Drucker
Hier habe ich dann doch die Abkürzung gewählt und die Form direkt gedruckt.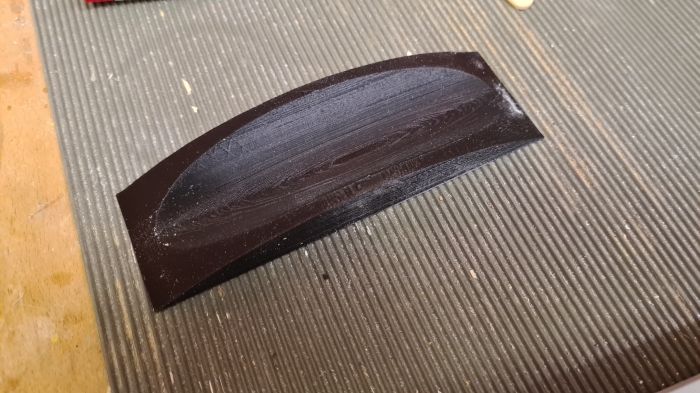
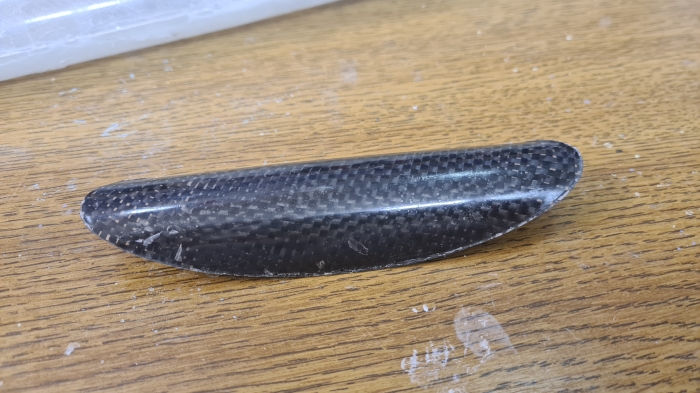
Erster Rumpf nach dem Lackieren
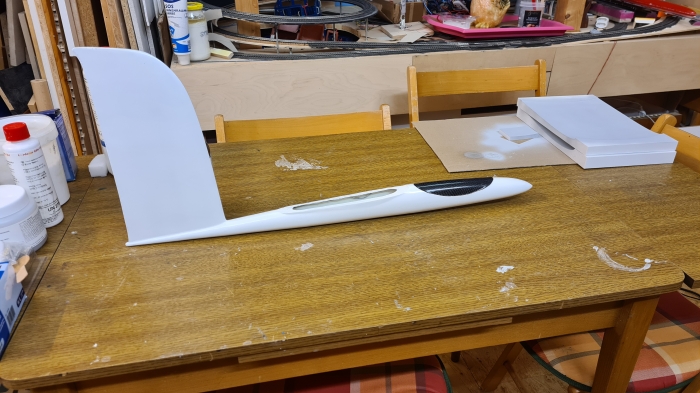
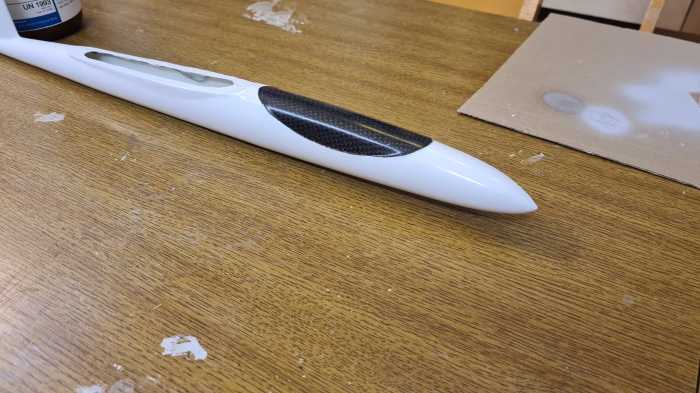
2m Tragfläche
Wird fortgesetzt...